Our Operations Director wins Women in Construction award
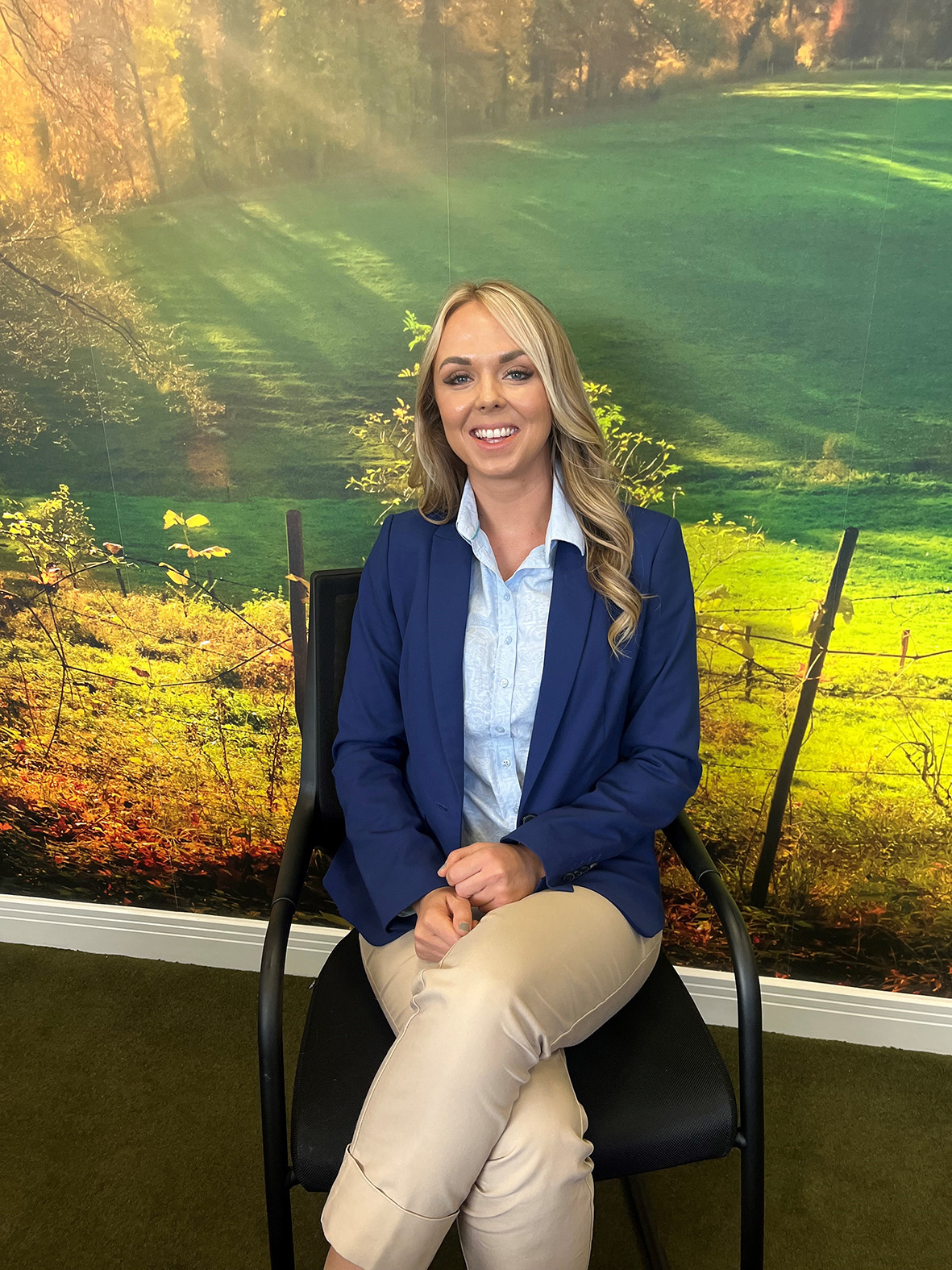
Our Operations Director, Charlotte Hale, has been named as winner of the Women in Construction category at this year’s Swansea Bay Business Awards.
The award was presented to Charlotte at the prestigious annual awards ceremony, held at the Brangwyn Hall in Swansea on the evening of Thursday September 15, 2022.
The Swansea Bay Business Awards cover the Swansea Bay City Region, incorporating the local authority areas of Swansea, Neath Port Talbot, Carmarthenshire, and Pembrokeshire. They celebrate the achievements of the talented and successful individuals, companies and entrepreneurs that work across the region.
The awards feature 11 individual categories with the addition of two awards given for overall Company of the Year and a Judges’ Choice Award for a firm that has demonstrated exceptional growth.
Charlotte was chosen from a shortlist of three talented and hard-working finalists in the Women in Construction category. Being chosen as the Women in Construction category winner, Charlotte has been recognised as an outstanding woman in the Swansea Bay City Region’s construction sector.
The award, sponsored by Pennant Homes, recognises Charlotte’s excellence in leadership and management, and highlights her as an exemplar and champion for encouraging more women to pursue a career in what has previously been perceived as a male dominated industry.
Charlotte Hale, our Operations Director and winner of the Women in Construction award, said:
“This is a great personal honour for me and, I believe, a recognition of the superb work the whole team at SO Modular are currently doing. The finalists in all the categories were of an exceptional standard, and so I feel I am in very special company to be chosen as the winner of the Women in Construction award.
“Construction is an industry that has long been perceived as a male dominated field of work. So, it is very heartening to hear the stories of the other inspirational female finalists in the category, and the great work they are doing in the construction sector – an industry that is open to all as a potentially fulfilling and rewarding career.”
SO Modular apprentice wins prestigious award
Here at SO Modular, we were proud to see apprentice Joe Munane recognised at the Swansea Bay Construction Support Group’s annual awards, held at the Village Hotel, Swansea, in July.
The ceremony is designed to support and recognise the achievements of new entrants, apprentices and future talent within the construction industry in the South Wales region.
Swansea Bay Construction Support Group’s overall objective is to promote the construction industry’s image and showcase the benefits of considering the construction industry as a career path, and what skills individuals can gain from this profession.
It works closely with Cyfle Building Skills, an organisation that manages a shared apprenticeship scheme in Southwest Wales for the construction industry. Some 90% of apprentices who complete the three years with Cyfle Building Skills secure full-time employment in their chosen trade.
Charlotte Hale, Operations Director at SO Modular, said: “We are delighted to hear that one of our fantastic apprentices has been recognised as a finalist for this prestigious award, and would like to formally congratulate Joe on his work with us. It has been an honour to watch his journey as an apprentice, and at SO Modular we really value his dedication and work ethic. We look forward to continuing to support Joe and celebrating all his successes within the construction industry in the future. Congratulations!”
Joe Munane said: “I have always wanted to work in the construction industry since leaving school and following the apprenticeship route helped me to do so. Currently, I am the lead designer for four live sites, and I have been given the responsibility to run those independently. When I finish my apprenticeship, I’d love to stay in the same role and keep gaining as much experience as possible until I’m ready to take the next step.”
Sheep’s wool insulation is used on innovative, ultra-low-carbon housing project
We are proud to announce that we have completed work on an innovative housing development with contractor Capsel and Monmouthshire Housing Association (MHA), to build 17 new homes across two derelict ex-garage sites in Pembroke Road and Western Avenue, Chepstow.
Both sites comprise of two housing types: a terraced mews style house with a patio area, and an interlocking courtyard bungalow. The innovative design concepts aim to address the specific housing ‘wants and needs’ of two definitive demographics: younger first-time buyers and older people wanting to downsize.
The low-carbon homes have been developed using £3.1m of funding by the Welsh Government’s Innovative Housing Programme. They are extremely energy efficient, with a Standard Assessment Procedure (SAP) in excess of 100.
The houses have been constructed using our closed panel timberframe system and also fitted with solar panels on the roofs and ground-source heat pumps to transfer natural heat from under the ground to keep them warm – eliminating the need for a gas supply.
The state-of-the-art project is the first to be completed using this exclusive closed panel timber system with natural Welsh sheep’s wool insulation, developed by us here at SO Modular.
The insulation is made from 75% sheep’s wool and 25% recycled polyester; a blend that allows for the full benefit of sheep’s wool with enhanced performance, breathability, durability, and sustainability.
This insulation has many benefits which will be enjoyed by the houses’ occupants: it regulates humidity, is mould resistant, has excellent sound reduction properties, and is breathable – purifying the air within the home.
Its convenient compressed form also reduces transport impact by more than 50% compared to other insulation and is recyclable.
At the forefront of innovative and creative solutions within the construction industry, we are pushing boundaries and developing products that boost efficiency, sustainability, and cost-effectiveness across a diverse range of construction projects.
Our current research and development projects consist of manufacturing carbon-neutral but affordable timber-frame homes; homes that are so thermally efficient, with U-values so low, they require minimal heating and cooling, potentially completely removing the need for a central heating system at all.
Charlotte Hale, our Operations Director, said:
“We’re very proud to have been involved in such a forward-thinking scheme implementing, for the first time, our innovative panelised timberframe system, incorporating Welsh sheep’s wool insulation. I’m sure that the benefits of this type of construction will soon be adopted by the wider construction industry as a way to sustainably insulate homes and reduce the carbon footprint of such projects.
“With the construction industry constantly changing to incorporate more environmentally friendly practices, and timber frame buildings fast becoming the norm across the UK, the use of these kind of forward-thinking alternatives is a positive encouragement for us here at SO Modular to continue researching, developing and adapting to meet modern housing demands.”
Stephen Venables, Senior Quantity Surveyor, Capsel Ltd., said:
“We extend our thanks to SO Modular on their service, support and professionalism when delivering the two schemes in Chepstow, South Wales for Capsel and MHA.
“Whilst this project, being a new design concept, experienced its challenges, SO Modular’s site team worked tirelessly to resolve any issues that arose and embraced the ethos of collaborative working between client, design and delivery teams. Their commitment, hard work and enthusiasm was incomparable.
“This development has been for us and MHA a great first experience utilising Natural Welsh Sheep’s Wool Insulation on-site, and I believe this being SO Modular’s first full scheme using such an innovative insulation, they are extremely proud of themselves – and so they should be.”
Business Development and Marketing Officer joins our team
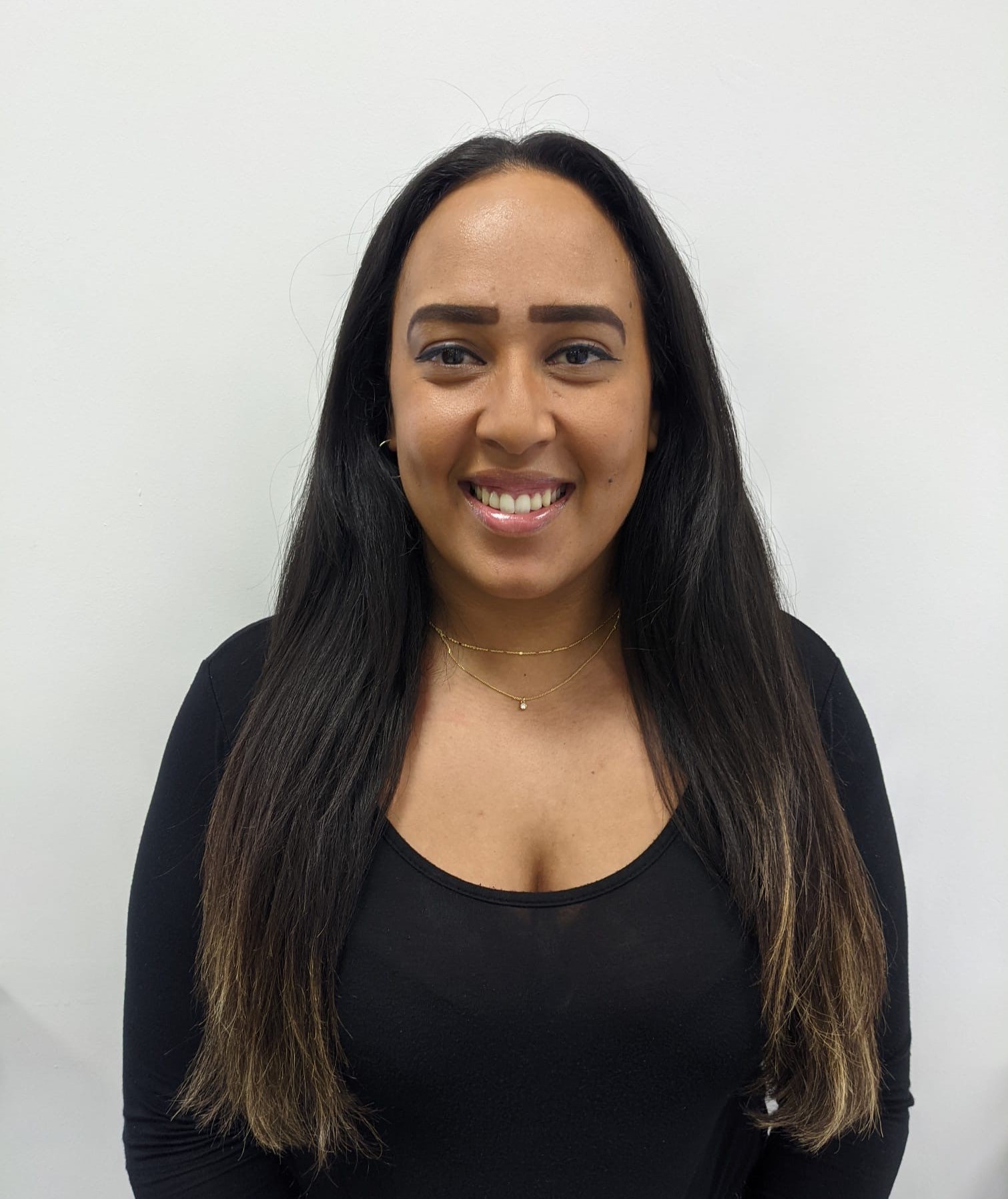
We have brought in a new Business Development and Marketing professional to join our rapidly growing team, here at SO Modular, to build and strengthen relationships with key stakeholders and the wider community.
Lisa Amphlett has been brought into the new role with the remit of creating, maintaining, and strengthening relationships with the wide range of SO Modular’s clients and partner organisations. These include housing associations, local authorities, main contractors, private developers, and national homebuilders.
Her role also sees her managing the company’s marketing initiatives, developing project leads, assisting with tender submissions, and organising engagement opportunities with the wider community.
As part of this wider engagement, Lisa also takes on the role of tenant liaison officer, based on-site at the County Flats development in Sandfields, Aberavon. Her remit in this role includes maintaining communications and developing relationships with the residents and wider community.
Amphlett joins us with five years’ experience within the construction industry in an office-based capacity. She has previously worked as a recruitment consultant for Involve Recruitment in Pontypridd, specialising in the recruitment of temporary construction site operatives. During this role, Lisa developed extensive experience liaising with clients ranging from multi-million-pound principal contractors to local trade specific sub-contractors.
Lisa Amphlett, our Business Development and Marketing Officer, said:
“I am delighted to be working at such an innovative and forward-thinking company as SO Modular, and I look forward to the challenges that lay ahead. I will be based at the County Flats development in Aberavon, and very much look forward to taking on the additional role of liaison officer at the site.
“My role with SO Modular is varied and my remit wide ranging, and I hope that the skills and experience I bring can benefit the company by increasing awareness throughout the industry and wider community of its innovative and sustainable products and working practices.”
Charlotte Hale, our Operations Director, said:
“We are delighted to have had Lisa come on board with us, here at SO Modular, as we look to accelerate our production capacity and develop our growing business. Her role is key to raising awareness of our products and services, and ensuring strong communications and relationships with our clients, partners and the wider community.”
SOM Sandfields project provides carbon-neutral homes using innovative methods and materials
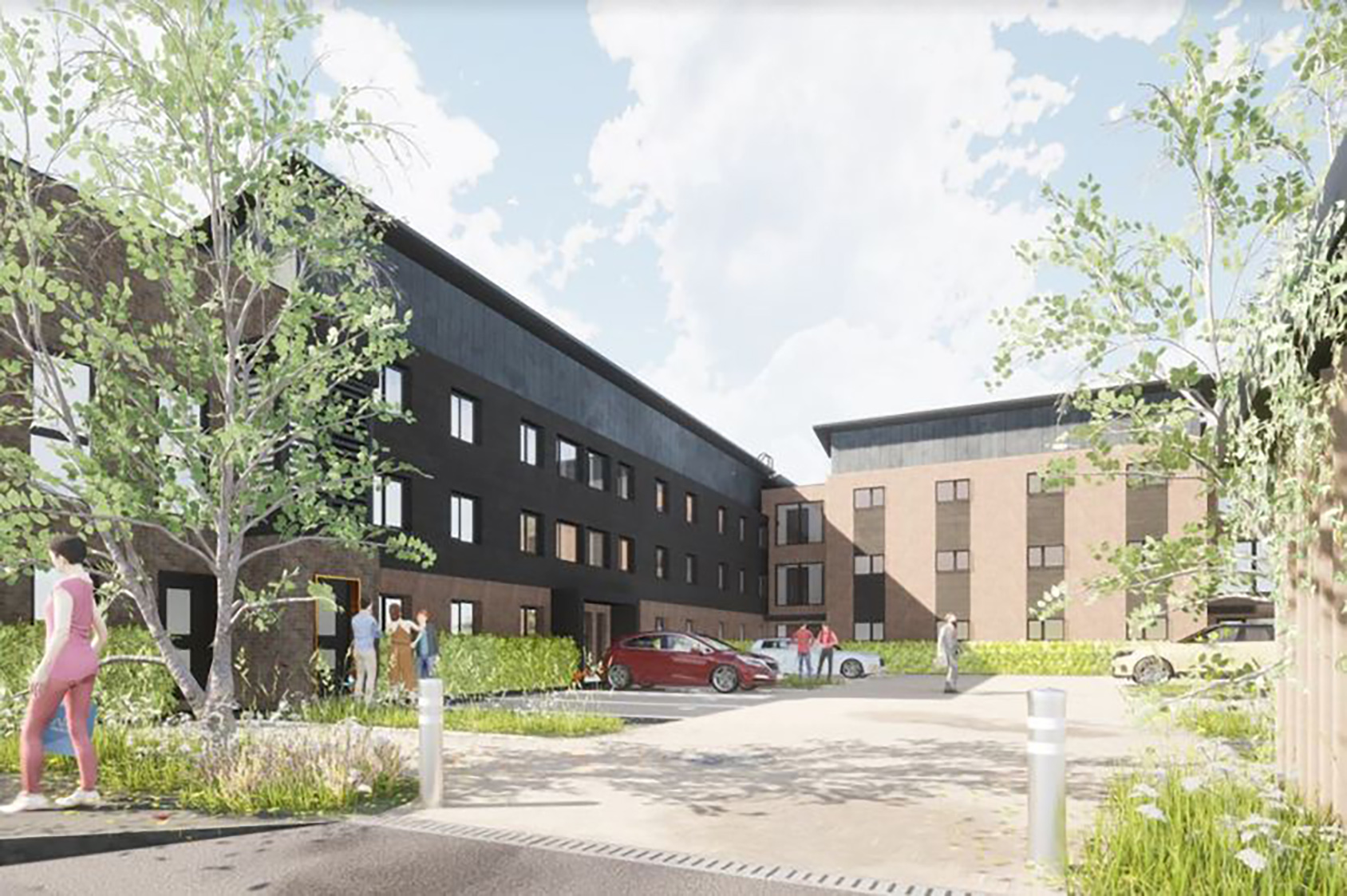
The new homes will be insulated using wood, wool, and mushrooms
Here at SO Modular, we are delighted to be collaborating with J.G. Hale Construction and Tai Tarian on a state-of-the-art project to build 55 new homes, and refurbish 72 existing flats, in Sandfields, Aberavon.
The scheme will eventually provide 127 carbon-neutral homes for social housing provider, Tai Tarian, delivered across three phases, over three years.
The project is a continuation of our existing relationship with J.G. Hale Construction and Tai Tarian, and is funded by the Innovative Housing Programme (IHP) – a Welsh Government funded programme to encourage and test innovative approaches to constructing social and affordable housing in Wales.
Construction of the 55 new homes and refurbishment of the 72 flats will be completed utilising modern methods of construction (MMC), including construction of all new homes off-site at our timber frame factory.
The scheme will achieve carbon neutrality via a range of in-house green and sustainable initiatives.
Most notable of these is the use of natural, eco-friendly forms of insulation made from three unusual and innovative materials: welsh sheep’s wool, locally sourced from Neath-based Crynant Farm; mycelium, the vegetative filament root structure of mushrooms; and a wood-fibre insulation developed in-house at SO Modular.
The pioneering insulation methods are providing a pilot study for the viability of their use in the wider construction industry.
As well as reducing the project’s overall carbon footprint, the use of these materials and technology aims to reduce fuel poverty for the development’s tenants by ensuring all homes are built with the top EPA rating of A.
A household is deemed to be in fuel poverty if, in order to maintain a satisfactory heating regime, it requires a spend of more than 10% of its net income on fuel, and in ‘severe’ fuel poverty if fuel costs are more than 20% of household income. Recent Welsh Government figures state that an estimated 155,000 households were living in fuel poverty during 2019 – equivalent to 12% of all households in Wales.
In collaboration with Neath Port Talbot College, the partnership will also be providing specialist, innovative traineeships, via their in-house training academy. The trainees will be supported by in-house mentors, who are specialists in their respective fields.
A range of Community Benefits will also be provided for the local community, coinciding with the Welsh Minister of Housing’s Wellbeing of Future Generations Wales Act, 2015.
Tai Tarian’s director of assets, Andrew Carey, said:
“County Flats is a prominent part of the Aberavon seafront. Built in the 1950s, the flats are looking tired and are in desperate need of updating. This development will do just that and will provide flats that will be amongst the most energy efficient and sustainable homes in Wales.
“It’s fantastic that we will be working with J.G. Hale Construction, who have committed to using local products and local people.”
David Harrhy, managing director at J.G. Hale Construction, said:
“We are delighted to be collaborating with SO Modular on this incredibly innovative project for Tai Tarian. The development, when completed, will be completely unique in its use of new sustainable materials and technologies, which we are sure will become more widely used within the construction industry.
“We fully support Tai Tarian’s objective to reduce fuel poverty for its social housing tenants, and by building all homes to the ultimate EPA rating of A, we will not only be helping the tenants save money on their fuel bills, but also be helping reduce energy usage, which is great news in tackling climate change.”
Charlotte Hale, our operations director, said:
“We’re very proud to be working on this collaboration with J.G. Hale Construction for social housing provider Tai Tarian. The use of these ground-breaking materials, along with our modern methods of construction, should set the standard for similar, future developments.”
“Our commitment to using local sub-contractors and training local people will, undoubtedly, improve the skills and opportunities for those in the Swansea and Neath areas, making the region the go-to place for knowledge on these new sustainable materials and methods.”
Our new Commercial Manager Gareth Whitney
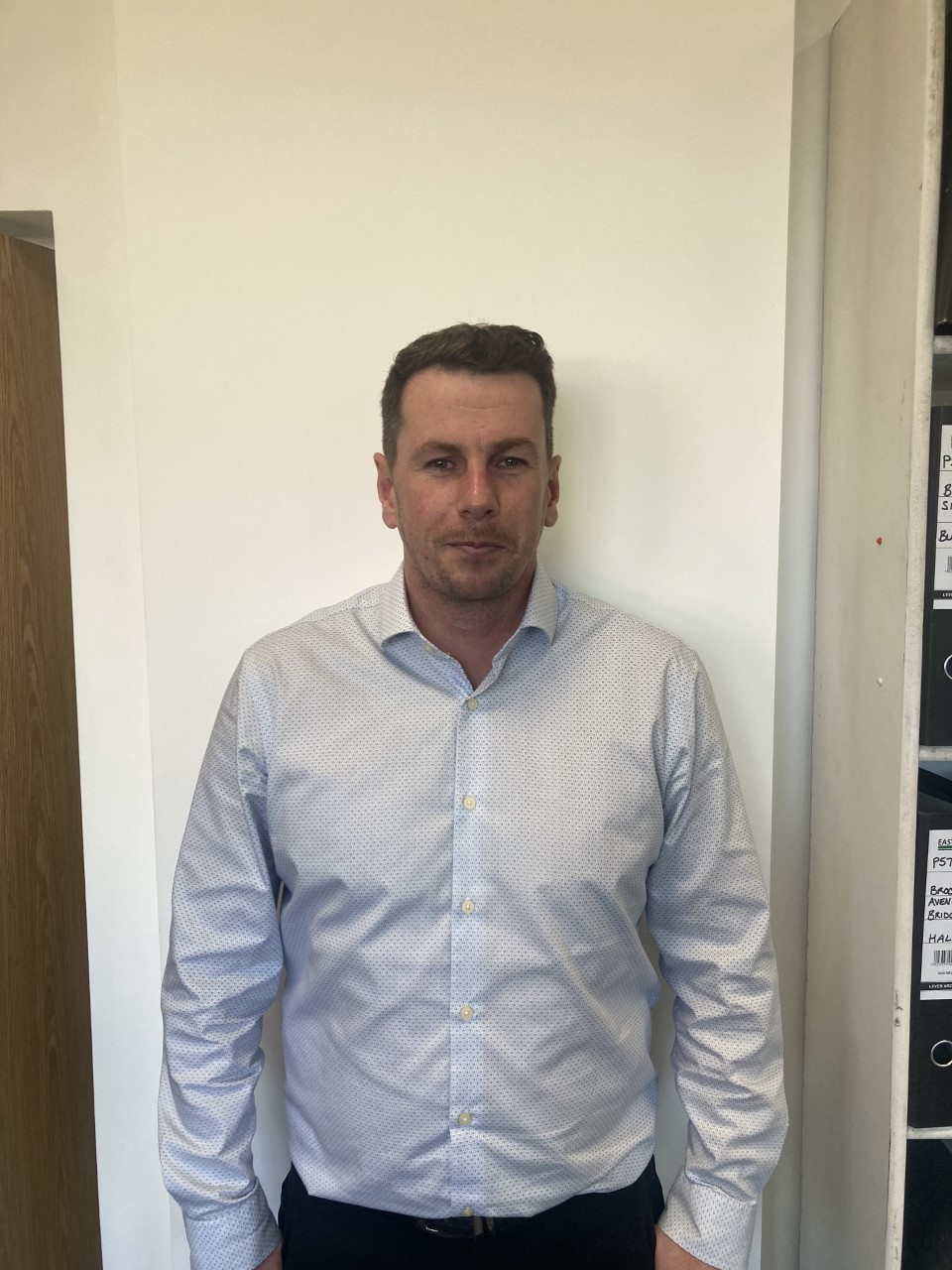
We are delighted to announce that we have strengthened our team, here at SO Modular, with a new senior appointment – Commercial Manager, Gareth Whitney – as we continue to expand our fast-growing, innovative and sustainable business.
Gareth has joined us to manage our commercial department and explore new commercial opportunities for the firm, as we gear up to increase production by 700% at our modular manufacturing facility in Milland Road, Neath.
Gareth comes to the role with 20 years’ experience within the construction industry: 17 years as an established Quantity Surveyor/Commercial Manager and three years as a Senior Quantity Surveyor.
During this time, he has worked for well-known construction firms Persimmon Homes, David McLean Homes, D&K Carpentry Contractors and, most recently, J.G. Hale Construction.
Gareth Whitney, our newly appointed Commercial Manager, said:
“This is a very exciting time to be taking on the role of commercial manager at SO Modular. The company’s new facility is ready to make the dramatic seven-fold leap in production capacity, so I am very keen to start developing new commercial opportunities and connections for the firm.
“Sustainability in building design and construction is vital if we are to start addressing our impact on the environment, so the future for innovative, sustainable, eco-friendly homes is incredibly bright. The way that SO Modular looks to improve its own carbon footprint at every turn is inspiring, and the way it is constantly looking to innovate makes the company very forward-thinking. This ethos is something that especially excites me about the company and my new role within it.”
Charlotte Hale, our Operations Director, said:
“It’s great to have someone with Gareth’s extensive experience on board at SO Modular. Gareth understands the construction industry inside and out and is passionate about ensuring the future of construction is sustainable. As such, we are sure he will do an excellent job working to develop our commercial opportunities and connections.
New skip hire division added to our expanding business
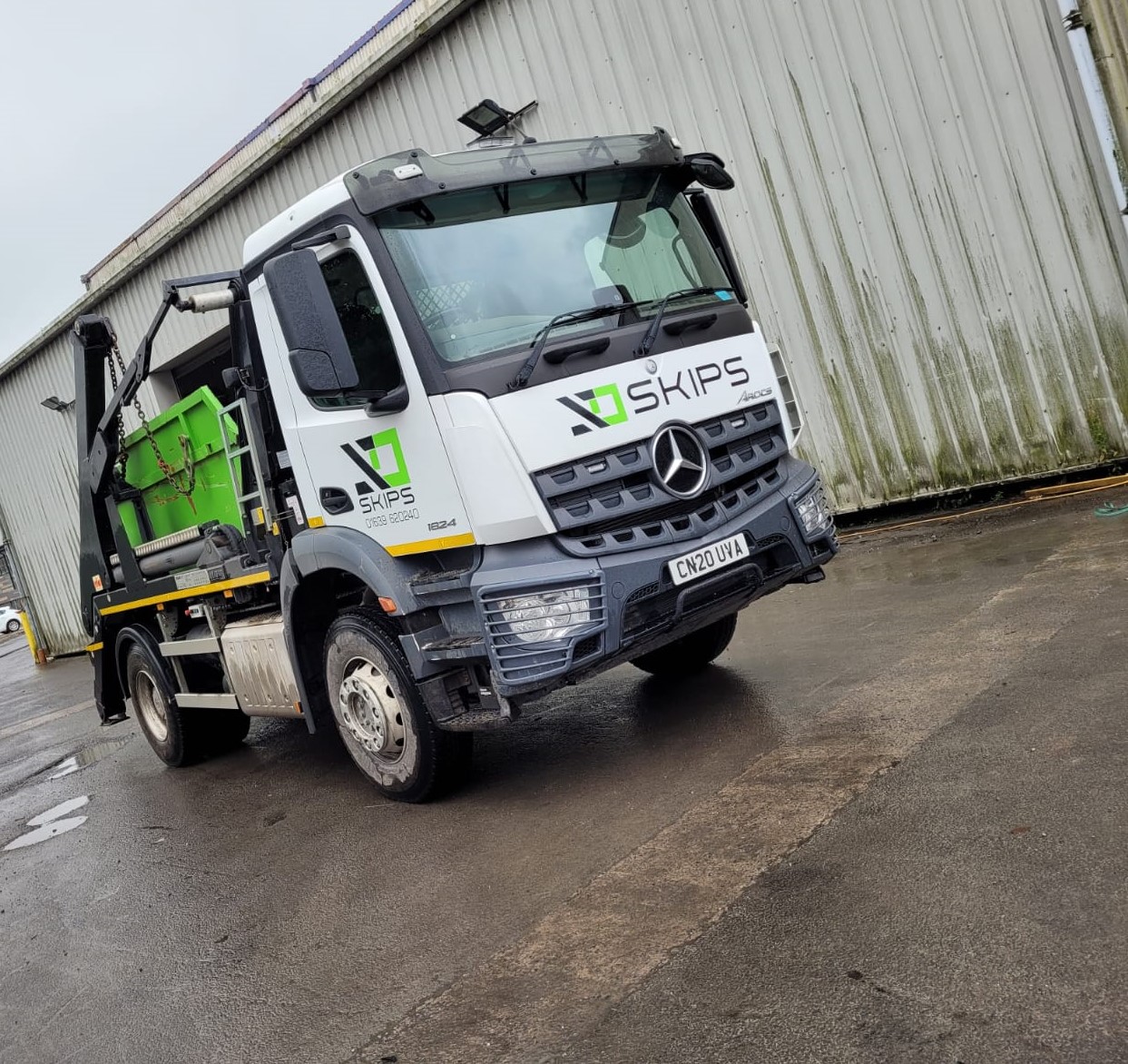
We’re delighted to announce that, here at SO Modular, we’ve added a new skip hire division to our ever-growing, innovative and sustainable business.
The new division, called SO Skips, will offer a variety of open skip sizes: 8-yard, 16-yard and high back 16-yard to both commercial business and private customers.
Timber wastage recovered from the skips will be recycled in our recently installed biomass boiler at our brand-new manufacturing facility in Neath, South Wales – further strengthening our commitment to sustainably manufacturing low carbon homes.
The recovered timber will be used to reheat the manufacturing facility, and avoid it being transported to landfill for disposal.
As well as heating the factory and offices, the biomass boiler is also used to dry treated timber in our new in-house treatment tank, helping us reduce our fuel costs and aiding in our goal to create a sustainable, renewable process for timber frame manufacturing.
Charlotte Hale, our Operations Director, said:
“This is a very exciting new division to launch for us here at SO Modular. That fact that we will be recycling all waste timber recovered from the skips means that customers know it won’t be going to landfill, making it a far greener option for them, and helping reduce their carbon footprint – which I’m sure is something we all want.
“With SO Skips, we promise very competitive rates and reliable, fast delivery and collection from our fully licenced service.”
Our production capacity will increase by 700 percent following our six-figure investment in new equipment
We have increased our production capacity by 700% thanks to our significant six-figure investment in new machinery at our new 350,000 sqft timber and modular manufacturing facility in Neath, South Wales.
The development of the facility began in April 2020 and is set for an official launch at the end of summer 2021. Once completed, with all the new machinery installed and running, the site will immediately be able to expand from its current production capacity of 500 homes per year to 3,500 homes per year on a single shift.
The timber and modular manufacturing facility will also be a zero-carbon, sustainable site, creating a number of skilled employment opportunities in the local area.
We have been able to fund the purchase of our new machinery through an Innovative Housing Programme (IHP) loan with Tai Tarian – one of the largest social landlords in Wales.
The new machinery is considerably more efficient – both in terms of speed and energy usage – than that currently being used. It will also produce less waste and will contribute towards us sustainably manufacturing low carbon homes.
The new machinery includes a treatment tank, Production Lines, a biomass boiler, a Hundegger TURBO-Drive II Saw, a vertical saw and a factory blow insulation machine.
The Hundegger TURBO-Drive II Saw will speed up timber processes, increase accuracy and reduce waste with the use of computer software technology. The saw’s optimisation software means that any offcuts it produces are automatically cut into smaller standardised pieces, which can then be used as other functional aspects of modular joist and cassette manufacture.
The biomass boiler will ensure waste timber is used to reheat the facilities, and avoid it being transported to landfill for disposal. As well as heating the factory and offices, the boiler is also used to dry treated timber in our new in-house treatment tank, helping us reduce our fuel costs and aiding us in our goal to create a sustainable, renewable process for timber frame manufacturing.
The new treatment tank will allow high- and low-pressure treatments, meaning we will be able to treat not only standard timber but also timbers that require a higher level of treatment such as sole plates. This makes it far more cost effective than imported pre-treated timber, helping us to achieve our affordable homes target.
Charlotte Hale, our Operations Director, said:
“We’re very excited to announce the purchasing and acquirement of new machinery, with the help of the IHP Tai Tarian loan.
“These new, efficient machines will go a long will in aiding us to establish a state-of-the-art, sustainable manufacturing facility in Wales. Furthermore, this acquirement will allow us to create new jobs in the area and provide even more affordable, low carbon homes to help the UK meet zero-carbon targets, protect the environment and address the country’s need for affordable housing.”
Economy Minister, Vaughan Gething, visits new facility
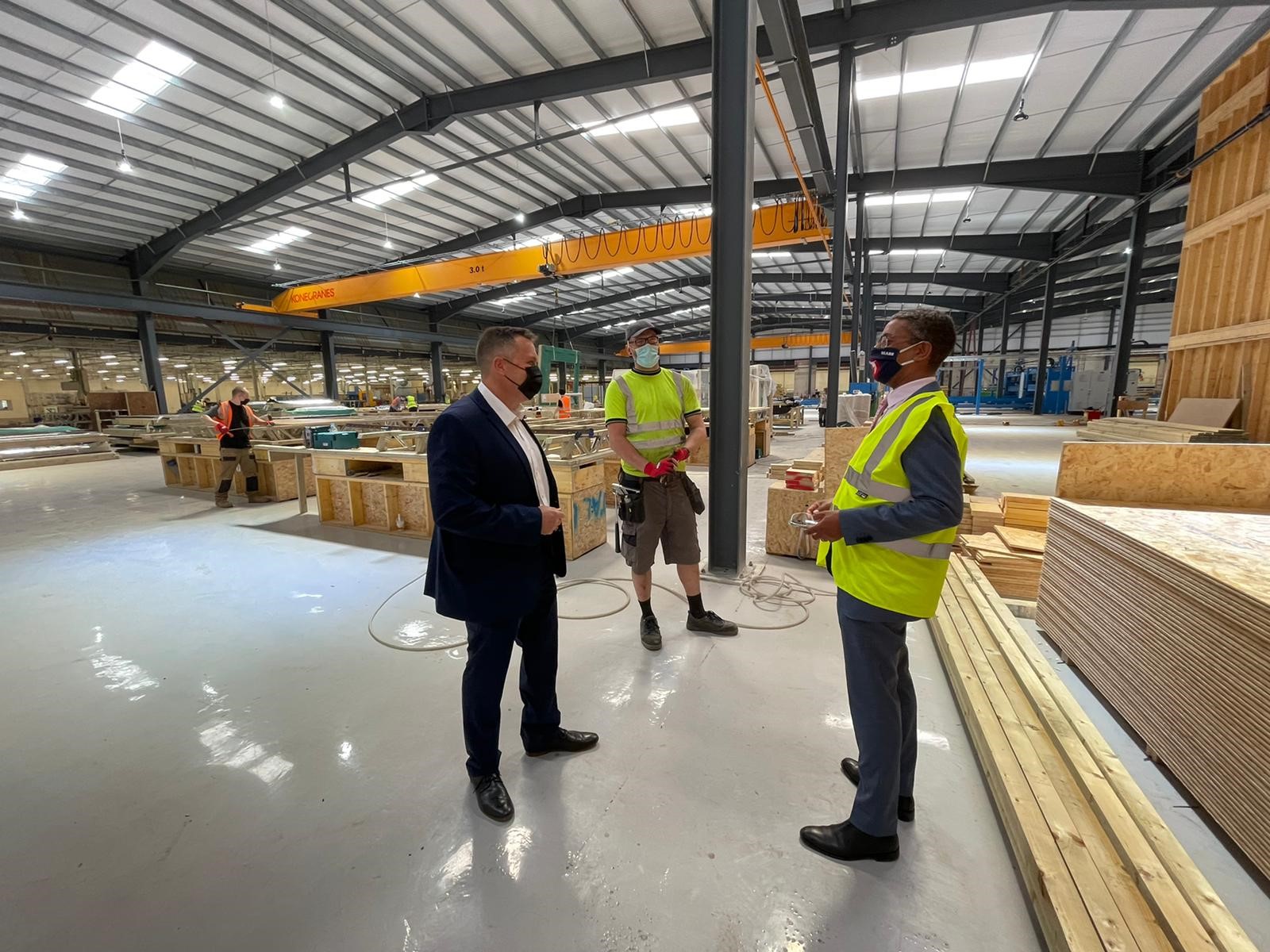
We were delighted to welcome the Economy Minister and Senedd Member, Vaughan Gething, to SO Modular’s new state-of-the-art, off-site manufacturing facility, located at the ‘Old Metal Box’ factory in Neath.
Mr Gething was given a guided tour around the new facility, ahead of its grand opening later in the year. During his visit, we showed him our latest investment in new equipment and explained our plans for the site – where we will be producing our sustainable, innovative, modular wood panel systems and roof trusses for use in the wider construction industry.
The regeneration of the ‘Old Metal Box’ factory into our new facility has been made possible due to a substantial £900,000 Property Business Development Gran through the European Regional Development Fundt.In addition, loan funding support worth over £2.85 million, provided through the Welsh Government’s Innovative Housing Programme (IHP) to Tai Tarian Housing Association, has facilitated further investment in plant and machinery to increase our capacity.
This increased capacity will allow us, here at SO Modular, to help tackle the local and national housing shortage, by creating affordable, sustainable, and environmentally friendly housing.
Senedd Member and Economy Minister, Vaughan Gething, said:“This government is committed to backing Welsh business and as we emerge from the Coronavirus pandemic one of my priorities is to kickstart Wales’ economic recovery, ensuring it becomes an engine for sustainable, green growth.
“SO Modular is a well-established company anchored in the local community. They are an important employer in the region, and I am delighted our support will help them to grow their business and further their decarbonisation ambitions.”
SO Modular and J. G. Hale Construction chairman, Jonathan Hale, said:“It was wonderful to be able to welcome Mr Gething to our brand-new site at the newly regenerated ‘Old Metal Box’ factory. The investment received through the Property Business Development Grant and the Welsh Government’s IHP scheme has made an enormous difference to SO Modular’s capacity.
Regeneration of the Old Metal Box factory and, subsequently, increasing capacity at SO Modular are both integral to the economic recovery Wales very much needs. The facility’s sustainable, eco-friendly products will also go some considerable distance to helping Wales achieve its future zero-carbon housing targets.”
SO Modular welcomes its new construction manager, Rhodri Perkins

We’re delighted to welcome the latest addition to the SO Modular team – our new construction manager, Rhodri Perkins.
Rhodri has extensive experience working within the construction industry over his 24-year career. Originally starting his professional journey as a qualified carpenter, Rhodri has steadily worked his way up to where he is today – an experienced construction manager.
Rhodri’s main area of expertise is in the construction of large accommodation blocks and housing projects for housing associations and private sales.
Having gained considerable construction experience with a variety of contractors over the years – including Morganstone and TRJ – Rhodri has held several managerial roles and is now set to play a key role in SO Modular’s timber frame and modular expansion, at a very exciting time of growth for the company.
Alongside his prior work for several prestigious companies, Rhodri has also run his own carpentry company for the last 20 years.
Speaking about his recent appointment with SO Modular, Rhodri Perkins, said:
“So far, my time with SO Modular has been really enjoyable and a real learning curve. I’m looking forward to progressing with my career and helping continue the growth of this great company.
“One particularly exciting development, which I’m really looking forward too, is the opening of our new state of the art modular and timber frame facility. We have some great plans and innovations on the horizon, here at SO Modular, and I cannot wait to see where we can go”.
SO Modular attains BOPAS accreditation
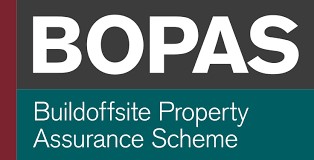
Here at SO Modular, we’re delighted to announce that we’ve attained BOPAS certification – an accreditation recognised by principal mortgage lenders as providing the necessary assurance to address the perceived risks associated with innovative construction methods.
The Buildoffsite Property Assurance Scheme (BOPAS) has been designed to address the issues associated with bringing innovative or non-traditional building methods and materials to the market.
Historically, mortgage lenders have been reluctant to lend against forms of construction with which they are unfamiliar. In many instances, valuers may have refused to value properties, as part of the mortgage application process, if the property incorporated unfamiliar building systems.
To address this issue, BOPAS has been jointly developed by Buildoffsite, The Royal Institution of Chartered Surveyors (RICS), Lloyd’s Register and BLP Insurance, in consultation with the Council of Mortgage Lenders (CML) and the Building Societies Association (BSA).
Accreditation by the scheme provides comprehensive assurance to mortgage lenders that innovatively constructed properties will be sufficiently durable as to be readily saleable for a minimum of 60 years – underpinned by warranty.
BOPAS certification lasts for three years, at the end of which BOPAS assessors will visit us to complete a two-day audit before recertifying. During the three-year period, BOPAS make two ‘surveillance visits’ yearly, with one focusing on the design and manufacture, the other an on-site visit monitoring construction.
Our current research and development projects consist of manufacturing carbon-neutral but affordable timber-frame homes; homes that are so thermally efficient, with U-values so low, they require minimal heating and cooling, potentially completely removing the need for a central heating system at all.
Charlotte Hale, our Operations Director, said:
“We’re very proud to have achieved this certification from BOPAS as a manufacturer and supplier. The scheme gives the correct assurances to mortgage lenders that our innovative products have the durability required to meet and exceed the BOPAS standards.
“With the construction industry constantly changing to incorporate more environmentally friendly practices, and timber frame buildings fast becoming the norm across the UK, BOPAS is a positive encouragement for us here at SO Modular to continue researching, developing and adapting to meet modern housing demands.”
Investing in new talent after uplift in demand
Here at SO Modular, we’re proud to be able to welcome a number of new recruits on the back of an uplift in work as we move into 2021, despite the challenges of the COVID-19 pandemic and subsequent lockdown.
Joseph Murnane joins us as a Trainee Designer and Harrison Davies as a Trainee QS. Both join as apprentices and we will work closely with Cyfle and Neath Port Talbot College to give them a rounded education and ensure they are fully qualified in their respective fields.
The course will mix classroom training with on-the-job experience, learning a number of skills in the process.
Harrison Davies, apprentice quantity surveyor, said:
“I am delighted to be a part of SO Modular. I am very excited to develop new skills, gain a plethora of knowledge from my colleagues and pursue my desired career in Estimating and Quantity Surveying.”
Joseph Murnane, trainee timber frame designer, said:
“I am happy to have started work here at SO Modular and I look forward to the challenges that lay ahead. I have already developed more knowledge and skills, including working the software needed for design, during the few weeks that I have been here. I have also learnt a lot about how the structure of timber frame is made. During my first year in college, I thoroughly enjoyed the design module, and this is why I wanted to start an apprenticeship based on design. So far, I have enjoyed the work that I have done at SO Modular.” Charlotte Hale, our Operations Director, said:
“We are enjoying a big uplift in demand as we move into 2021 and we are excited to be able to offer young people this opportunity. We look forward to watching our new apprentices grow with our company in 2021 – giving young people a chance is important in these challenging times.”
What is Passivhaus
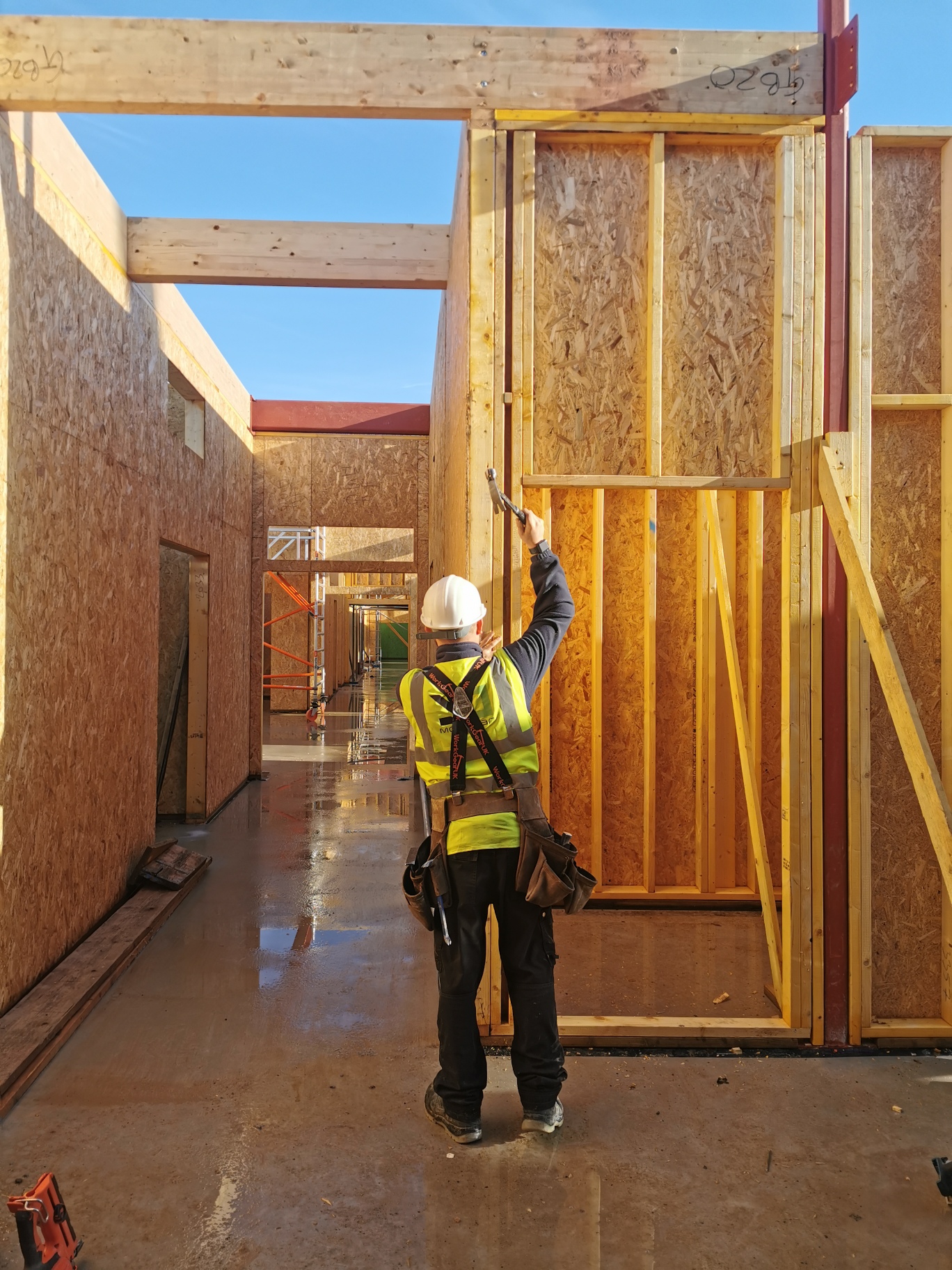
Here at SO Modular, we have invested heavily in training all our employees in our fitting teams to educate them around the importance of air tightness and Passivhaus standards. We are also delighted to be working with Lloyd & Gravell on two new school builds that will embrace Passivhaus standards.
The Passivhaus concept was devised by Dr Wolfgang Feist who completed a great deal of research into the amount of energy consumed in buildings. He found that the energy consumed was often much higher than originally predicted.
On the back of his work, he developed a building standard that is truly energy-efficient, comfortable and affordable. The first building built with these standards in mind was built some 25 years ago in Darmstadt, Germany.
The concept means that buildings must make efficient use of the sun, internal heat sources and heat recovery, making conventional heating sources unnecessary even in the coldest winters. It also means that buildings must have good indoor air quality, a ventilation system to supply fresh air and a low carbon footprint.
While the upfront cost of a Passivhaus building might be higher, they consume up to 90% less energy compared to a conventional building, dramatically reducing the whole life operational carbon emissions and running costs.
There are increasingly stringent standards and certification criteria around this form of building, which we support wholeheartedly.
Charlotte Hale, our Operations Director, said: "Everything we do at SO Modular is guided by environmentally friendly principles and we believe that Passivhaus principles will become ever-more important and pervasive in the construction industry. That is why we have made the investment we have and are always delighted to work on projects that embrace these standards."
More about the Passivhaus concept can be found here: Passivehaus Trust
Investing in our people: Passivhaus training

Here at SO Modular, we are delighted to say that all the employees in our fitting teams have now taken and passed an in-house training programme, designed to educate them around the importance of air tightness and Passivhaus standards.
Passivhaus standards relate to the energy consumed by buildings and the extent to which they are energy-efficient, comfortable and affordable, applying stringent standards and certification criteria to buildings.
The training was carried out by specialist design and manufacturing engineer, Verity Moorhouse, who we are working with us as part of a Knowledge Transfer Partnership, a Welsh Government initiative designed to help companies innovate by matching the skills and expertise of individuals in higher education with companies.
The initiative also represented an important landmark in our journey to establish a formal training academy at our headquarters, the former Metal Box Factory, in partnership with Neath Port Talbot College and Cardiff Metropolitan University.
The Passivhaus training programme enabled us to collect invaluable feedback from staff on the best way of creating a training academy on site with a view to launching the best learning facility for Offsite Manufacturing in the UK.
Charlotte Hale, our Operations Director, said: “We believe in the importance of training the next generation and the value of quality in everything we do. A training programme like this helps instill these values in our people, and ensures our staff are trained correctly.
“We understand that without the right training in place we cannot achieve the best results. Our aim is to inspire future generations to believe in producing a quality product and protecting our environment.”
Dedication and training: celebrating success with our staff
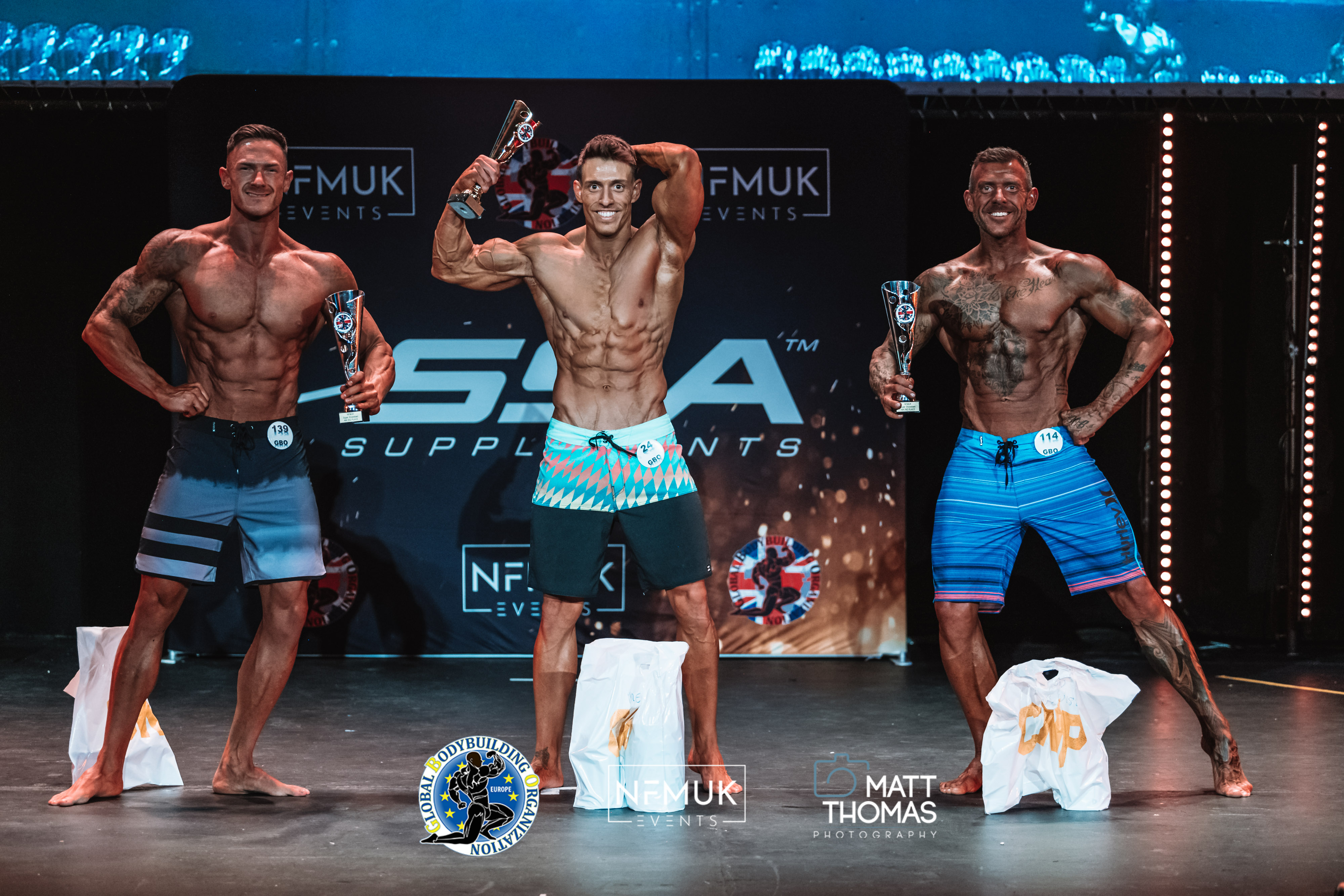
Here at SO Modular, we know that we are only ever as good as our people. We aspire to work with individuals who are hard-working, motivated and always go the extra mile – in all aspects of their lives.
We are also incredibly proud of our people’s achievements outside work. So, we want to give huge credit to Josh Collins, one of our senior estimators, who has featured in his first professional bodybuilding competition – and come back with a number of medals and accolades.
In his first NFMUK event (the UK promotor of the Global Bodybuilding Organization), Josh placed in four categories: 1st in the Men’s Fitness category, 2nd in the Beginners Men’s Fitness category, 2nd in the Men’s Beach Category and 2nd in the PRO Men’s Fitness Category.
Because it was his first event, Josh, who trains at Neath Sports Centre, started the evening by entering the beginners’ categories. However, after doing so well, he was awarded his ‘PRO’ card that day and was allowed to compete again later that evening against other PRO Status competitors.
Charlotte Hale, our Operations Director, said: “We are so proud of Josh and his achievements. We always support our people in every way we can, and it is amazing to see Josh achieve so much in a sport that is his passion and requires such dedication and hard work.”
Applying Passivhaus standards to two new school builds
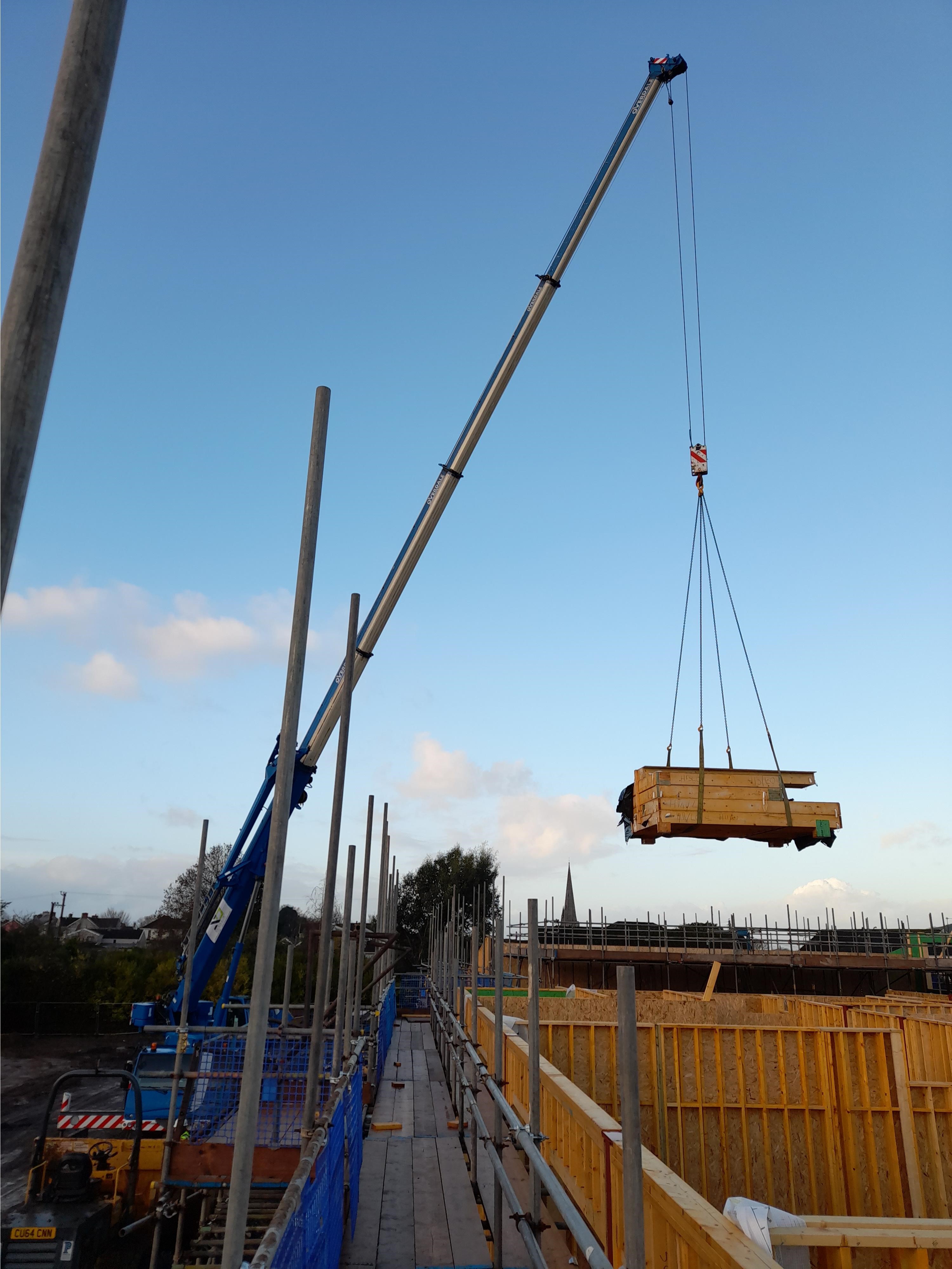
Following a significant investment in training our staff to understand and adhere to Passivhaus standards, we are delighted to be working on two exciting projects with Lloyd & Gravell that will embrace those standards.
A new 270-place, English-medium primary school with 30-place nursery and up to 23 full-time places for Early Years provision, is being constructed adjacent to the current Ysgol y Castell in Kidwelly. The current facility will be demolished on completion of the new build to accommodate a MUGA sports field and car parking area.
We are also delighted to be working on the Ysgol Gorslas project with the company, a new £6.8million project that will create a new 210 pupil capacity school building on land located behind Gorslas Community Park. Both schools will be built to a BREEAM Excellent, and energy efficient Passivhaus standard
The scheme will provide space to accommodate nursery provision and facilities which can be shared by the community such as a large hall, school field and a multi-use games area. It is hoped the new school building can still be completed by Spring 2022.
The project has been developed as part of Carmarthenshire County Council’s Modernising Education Programme (MEP) in collaboration with the Welsh Governments 21st Century Schools Programme.
For both schools, SO Modular will build and install a timber frame structure including all steel and glulams required for the buildings as well as installing insulation to Passivhaus standards.
Charlotte Hale, our Operations Director, said: "These are two fantastic projects to be working on. It is always great to be creating buildings that will play a vital role in educating and inspiring future generations. Evermore so when working with a partner such as Lloyd and Gravell who are such a remarkable Contractor to work with.
“We are also delighted to be able to apply Passivhaus standards to these builds. We have invested in training out staff in these standards and we look forward to putting that investment into practice.”
Leading the way on sourcing wood locally – and helping others do the same.
Governments and local authorities are increasingly seeking sustainability – in all types of policies but especially construction. This means more timber frame homes and also carefully considering where and how the timber is sourced.
Here at SO Modular, we are proud of the fact that the timber we use is sourced locally. The majority comes from our own doorstep in the Neath Valley, milled by Pontrilas Sawmills, just over an hour away in Hereford. Founded in 1947, Pontrilas is one of the largest independent sawmills in the UK as well as one of the most advanced and technically automated in the country.
We use enough wood every year to build more than 1,000 timber frame homes. This amount is set to increase exponentially as our business grows rapidly and demand for timber frame solutions soars.
Since our investment in the Metalbox Factory in Neath, we have capacity to make more than 3,500 homes a year. As such, we are seeking new sources of timber in Wales.
Timber frame homes offer many advantages including more environmentally friendly and energy-efficient credentials. Their carbon footprint is considerably smaller than other construction methods as they require less materials and labour, which results in less machinery.
They are far faster to build than a traditional brick and mortar house. All of the timber frames can be constructed off-site quickly (undisturbed by bad weather) and transported to sites, where they can be erected promptly and efficiently.
More and more tenders are now starting to emerge in which it is specified that the wood for timber frame homes is sourced locally. To which we fully endorse.
These local initiatives intersect with the wider aims and objectives of the Welsh Government. In its Future Generations Act, Wales has set out a vision to increase environmental, social, cultural and economic wellbeing in the country. On 29 April 2019 Welsh Government declared a climate emergency and subsequently published a 10 Point Plan to Fund Wales’ Climate Emergency.
Consequently, it pushes for a change in the countrys policy that will increase forestation (approx. 4000ha per year until 2050) to sequester carbon and increase timber for use in construction. The aim is to create high-performance and affordable new timber homes while supporting local manufacturers and suppliers.
Responding to this, Woodknowledge Wales along with the Welsh woodland organisation, Coed Cymru, Cardiff Metropolitan University and BM TRADA, established the Home-Grown Homes project. The project’s purpose is “to create high-performance and affordable new homes from wood in a manner that maximises the opportunity for local manufacturers and home-grown timber.”
As part of the Home-Grown Homes partnership, one local authority, Powys County Council, has adopted a Wood Encouragement Policy. The mission is to “build better, more energy efficient houses, support the local forestry industry and to create jobs. The policy sets out that all new council housing projects will look to use wood as the preferred material for both construction and fit-out purposes.”.
Charlotte Hale, our Operations Director, said: “The policy is the first of its kind in the UK but it is likely others will follow. Here at SO Modular, we remain committed to leading the way in developing a sustainable and environmentally friendly supply chain that aligns with these policies and objectives. We are exploring all avenues of ensuring that we continue to source wood locally and work with all relevant parties to make this a reality. SOM are very proud to say that they currently nearing completion on the first of its kind, all Welsh Timber Frame project in Brecon for Powys County Council.
New biomass boiler is a step towards embracing the circular economy
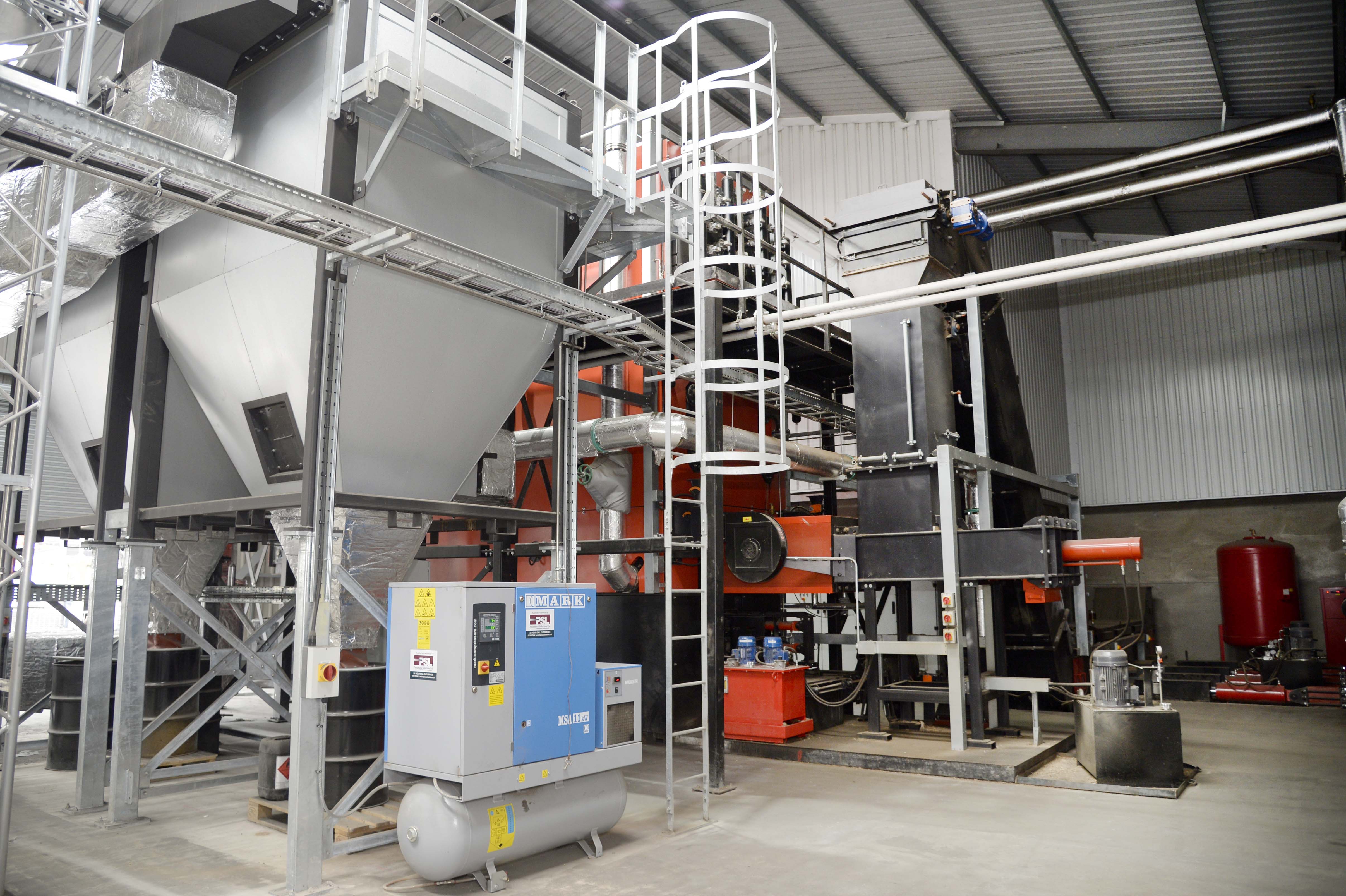
Here are SO Modular, we are delighted to unveil our new biomass boiler at our headquarters, the result of a significant investment but one which moves use closer to becoming completely self sufficient in terms of our energy and our production process.
The cutting edge biomass boiler was installed by energy specialist Novalux Energy. It is fuelled by our offcuts and wood shavings, a natural biproduct of the production process and will re-use 90% of the fuel into usable heat.
It works by burning the fuel at high temperatures to produce heat, or thermal energy. This thermal energy is transferred to a heat exchanger which provides you with heat for space or processes. The technology also utilises carbon filters to filter out impurities in its emissions to ensure they are not harmful to the local environment.
The installation means that we now recycling a very high percentage of our waste material, converting it into energy. We are now almost self-sufficient in our energy needs during production and even have surplus at some points in time, which we sell to the grid.
Charlotte Hale, our Operations Director, said: “We are embracing sustainability in all aspects of what we do and the biomass boiler is just the first of several initiatives we have planned including solar panels. We believe this will be a fantastic case study for the benefits of the circular economy.
“Our aim is to sustainably redefine the buildings we construct and restore our new facility to its former glory but in an innovative and eco-friendly way; we want it to be a landmark of the town again, which the community can be proud of, while also benefiting the local supply chain and keeping jobs and money in the region.”
SO Modular celebrates win at regional awards
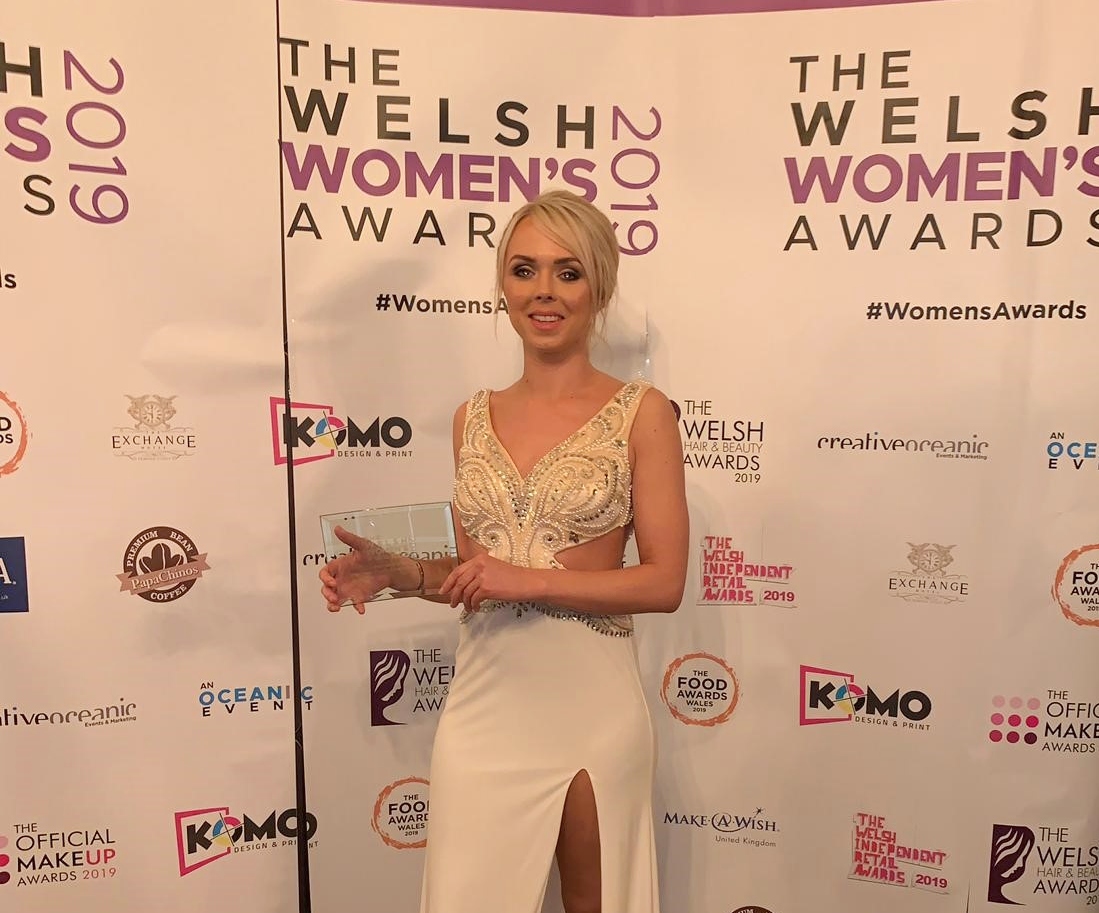
Celebrating its rapid growth and commitment to innovation, SO Modular Ltd has been named as one of the winners at The Welsh Women’s Awards, which took place on 3 April.
The awards, which took place at The Exchange Hotel, Cardiff, recognised Charlotte Hale, director of SO Modular, as the winner of the Entrepreneur of the Year award for her commitment to developing and growing the company since its launch in June 2018.
SO Modular continues to be at the forefront of innovative and creative solutions within the construction industry, pushing boundaries and developing products that enable it to boost efficiency, sustainability and cost-effectiveness across a diverse range of construction projects.
Its current research and development projects consist of manufacturing carbon-neutral but affordable timber-frame homes. These thermally efficient homes have U-values so low, they require minimal heating and cooling, potentially completely removing the need for a central heating system at all.
Charlotte Hale, director of SO Modular, said:
“I am thrilled to have won Entrepreneur of the Year at The Welsh Women’s Awards. I am passionate about making SO Modular an innovative, environmentally friendly and sustainable company – with the aim of making our planet as sustainable as can be.
“We have some really exciting plans for the next 12 months that will see SO Modular expand, grow and create more jobs, which in turn will support the local economy.”
The Welsh Women’s Awards, run by Creative Oceanic, is just one of the categories of awards run by the event host. Creative Oceanic operates and delivers events such as The Welsh Women’s Awards in nine different cities across the UK, Ireland and Canada. Some of the award ceremonies it runs in Wales are: The Welsh Hospitality Awards; The Welsh Wedding Awards; The Food Awards Wales; and The Welsh Independent Retail Awards, to name but a few.
Prostrate Cancer UK
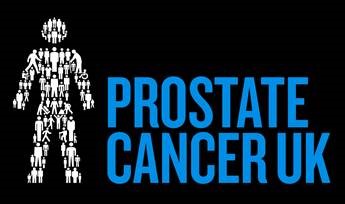
SO Modular are raising money in aid of Prostate Cancer UK.
A team of 20 members of staff are doing the Pen Y Fan climb on Sunday 24th March.
Please follow the link below to our just giving page. We would be grateful for any donations:
Just GivingChiltern in progress
Movember

November is approaching and we will be raising money for the Movember Foundation to support mental health and cancer.
Our staff will be paticipating in this event and for anyone who would like to get involved are welcome too.
Visit our team page in the link below to donate, see more information and join in!
moteam.coNew brand, new website
Seven oaks Modular has been rebranded with thanks to Techmeleon
A new modern website and technelogical updates to its processes will ensure SOM will continue to be a leader in the timber frame sector manufacturing sector.
Seven Oaks Pricing
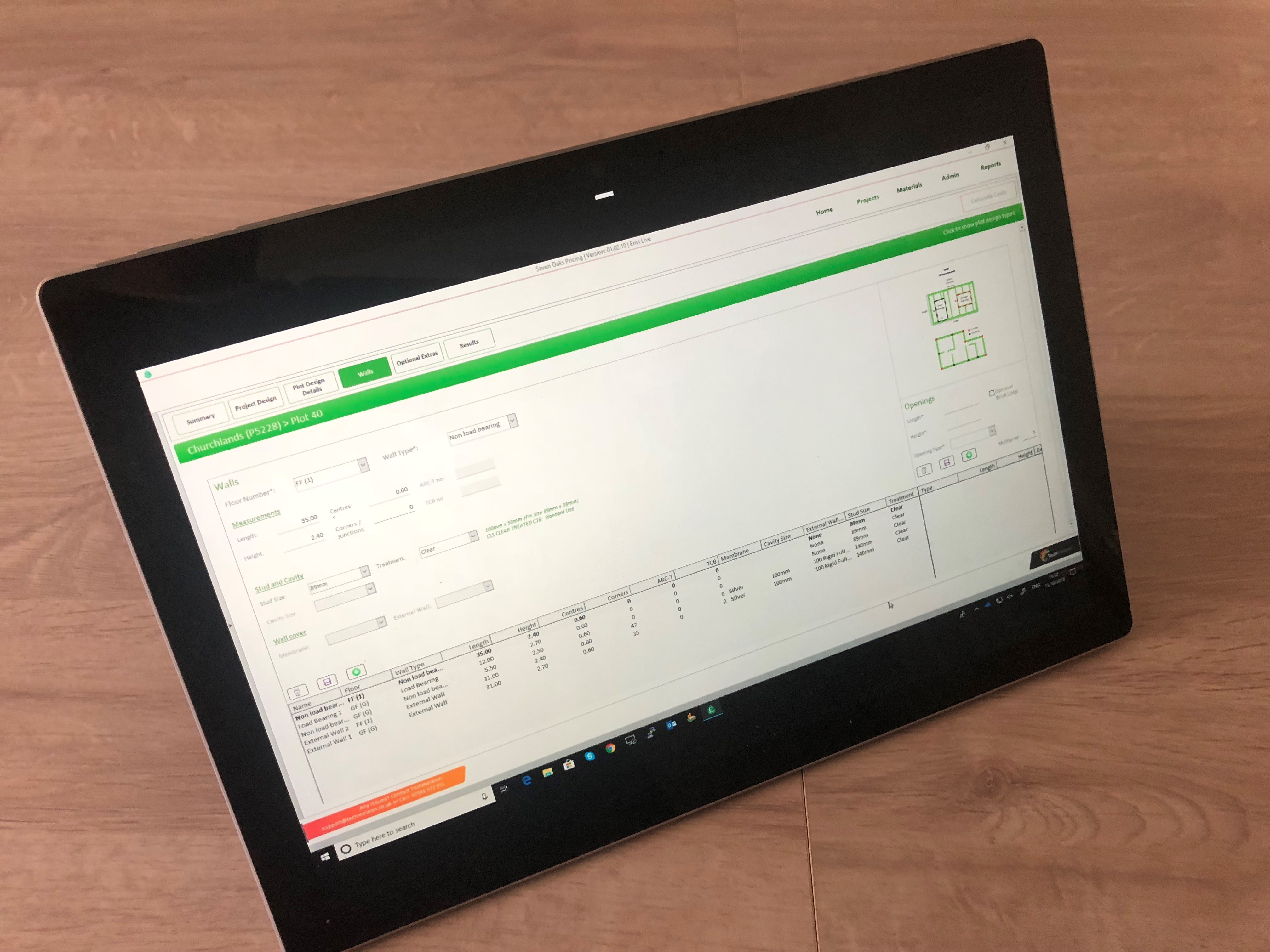
SOM have commissioned a new pricing system for the quotation process of tenders. With the assistance of Techmeleon a fully dynamic, structured and adaptable system has been created to produce competative, fast & accurate pricing.
Neath based timber company set to grow by 5 million
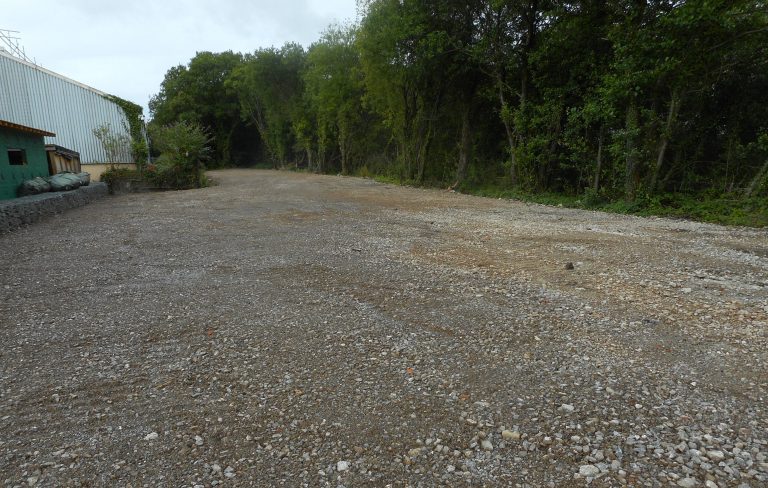
Seven Oaks Modulars, the award-winning Neath based timber frame manufacturer, looks set to reach its £6million growth target as it doubles its factory space and invests in new staff and equipment.
The company has recently purchased one and a half acres of land adjacent to its existing one acre site. The new space will be incorporated into the current site to create a high end, purpose built environment to store and prepare timber frames.
At present the company produces enough panels to make 12 homes a week, but it is planned that by the end of 2018, that number will double. To enable the increase in output, a £300,000 investment has been made to purchase a new eco press, and £100,000 in new lorries.
Seven Oaks has also invested in new marketing staff, 10 new lorry drivers and two new trainee timber designers. The trainee designers will work across projects for local authorities, private contractors and housing associations, as the company expands its remit and reach across the UK.
Seven Oaks Timberframe currently supplies timber frame and composite construction solutions to major house builders and construction companies across the UK.
It also supplies all the frames required by sister company J G Hale Construction; playing a contributing role in the construction company’s recent success at the LABC South Wales Building Excellence Awards.
The growth has largely been driven by Seven Oaks Timberframe’s development of Triso-warm, an innovative type of insulated timber frame that has the capacity to significantly reduce heating and energy bills.
Earlier this year, Triso-warm became the only UK produced timber frame of its kind to gain BBA approval – the stamp of approval required by the construction industry.
Chairman of Seven Oaks, Jonathan Hale commented:
“This is a really exciting time for Seven Oaks Modular. We have spent a long time building up our staff expertise and investing in the right equipment to produce Triso-warm frames. Now the time is right to take what we’ve achieved and significantly increase our output. Having the extra land, new drivers and designers joining will enable us to make the leap a reality.”
Seven Oaks attends the Explore Offsite South West Conference in Exeter
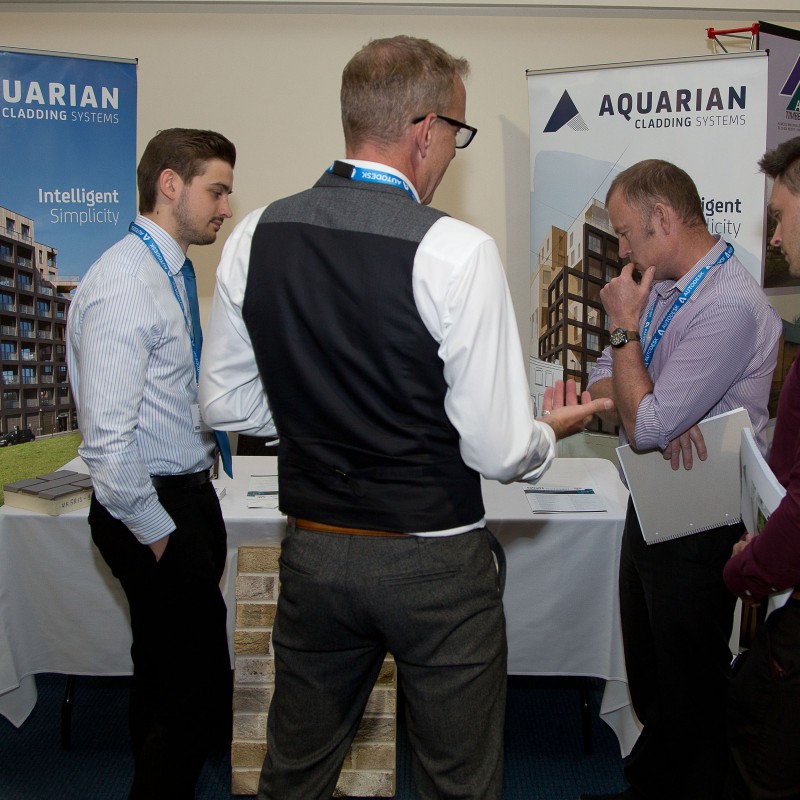
Explore Offsite Exeter – Two members of our team at Seven Oaks recently attended the Explore Offsite South West Conference in Exeter. Senior Designer Warren Rowlands and Business Development Officer Robert Spear met with various offsite organisations to gain further knowledge and insight into the Offsite modular movement, which is showing great opportunity within the construction community in the UK.
Seven Oaks moving forward are looking to introduce more bespoke modular products in to their range as the UK housing market leans towards offsite production as a means to counteract a skills shortage within the construction sector.
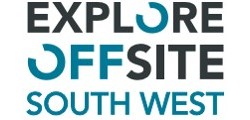
Triso-Warm achieves BBA approval
Seven Oaks, wales leading timber frame manufacturer and supplier, has been granted approval by the british board of agrément for Triso-Warm®, an innovative timber frame building panel which has the capacity to cut heating and energy bills to virtually zero. Triso-warm achieves ultra-low u-values with high strength panels, promoting off-site manufacture with factory controlled quality.
Always insist on BBA approved panels
Third party certification is extremely important for construction products. Certification means that an independent body has reviewed the manufacturing process of a particular product. It has been independently determined that the final product complies with safety, industry standards. Quality and conforms to british and european standards.
This valuable third party endorsement for a product’s performance gives specifiers and contractors extra reassurance that products have been rigorously tested.
Seven Oaks Timber Frame are proud sponsors of the 2016 Building Excellence Awards
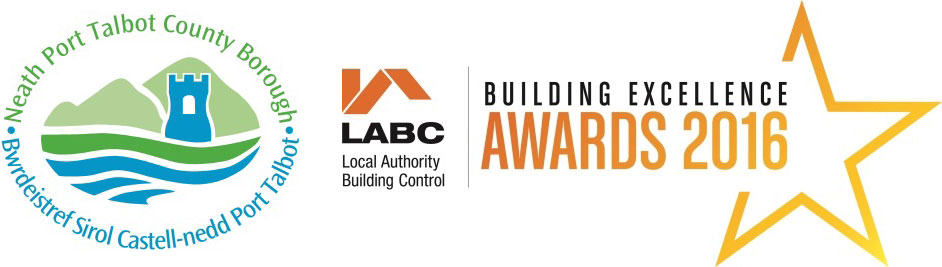
For the second year running Seven Oaks are proud to be the main sponsor of the labc building excellence awards a prestigeous event for professionals to be recognised and celebrate their achievements in the construction industry. They reward excellent buildings, outstanding companies, and partnerships and individuals that go that extra mile.
The LABC network covers all local authorities in England and Wales and is split into 12 regions, each of which holds their own awards.
Unlike other awards, it’s not all about looks! LABC consider other vital elements including:
- High levels of compliance with building regulations
- Effective working relationships with LABC surveyors
- Outstanding craftsmanship
- Technical innovation
- Sustainability and high performance
- Ability to solve technical problems with creative solutions
- Use of innovative products and the skills to overcome difficult site conditions
Regional winners in each category are automatically shortlisted for the LABC Grand Finals which are held in London.